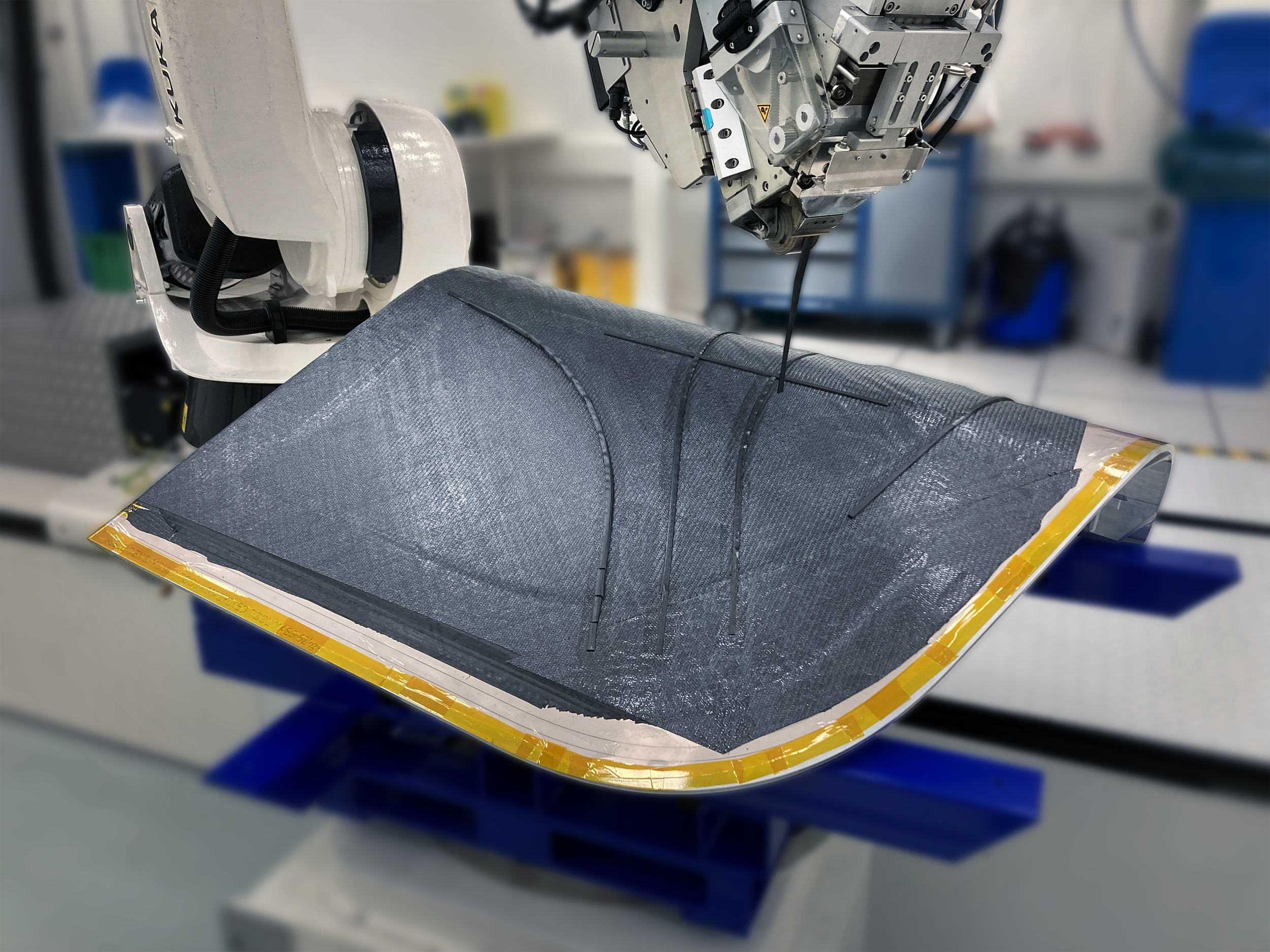
Pioneering more sustainable aircraft cabin structures
How a breakthrough method of creating composite structures could be key in advancing industry sustainability goals
As airlines look toward fulfilling Net Zero 2050 goals, sustainability continues to be an imperative within the aircraft interiors industry.
Among those contributors to sustainability under focus, development of lighter cabin components is the most obvious. Every gram or ounce saved translates to improved fuel efficiency and reduced emissions, driving the industry to explore innovative solutions to reduce weight.
Sustainability is a guiding principle for the work done by the Collins team based at the RTX Technology Research Center, the innovation hub for RTX and its businesses.
“With this big push toward sustainability, we’re rethinking how we use material and build structures,” explains Brian St. Rock, Director of Advanced Technology and Laboratories. “We’re taking it back to the underlying principles and the physics of what we do.”
The team's development of a new structural technology, named STARLight™, represents a significant sustainability breakthrough.
Rendering of a business class seat shows how STARLight can be incorporated as part of the underlying structure.
The ultimate play of form and function
STARLight introduces a novel method for using composite material to craft cabin structures. While composites aren’t new, STARLight structures stand out in how they are designed and produced.
Unlike traditional structures, where pre-manufactured honeycomb panels are assembled by cutting away unneeded areas, STARLight takes an additive approach. This means the structure’s shape is customized to performance requirements, and composite material is added only where it’s needed. The resulting form is monolithic (a single piece instead of multiple pieces attached together) featuring clearly visible rib structures designed to bear load and stress.
With reinforcing stiffeners added only where needed, the STARLight structure is thinner yet maintains strength and durability. It’s also lighter, to the tune of a 20% reduction in weight compared to honeycomb material. In a world where grams matter, the weight savings is significant.
A side-by-side comparison of an AirLounge business class seat shell. The shell on the right uses traditional materials, while the shell on the left was created with STARLight composite material.
A more sustainable manufacturing method
Where STARLight unlocks new dimensions of sustainability lies in its manufacturing process. Automation and robotics are used to create structures more efficiently. And through the nature of additive manufacturing, where material is applied only where it’s needed, little material goes to waste.
With this minimal material waste and a nearly 1:1 buy-to-fly ratio, the efficiencies with manufacturing STARLight structures replaces traditional energy-intensive manufacturing processes.
This additive manufacturing process also eliminates the need for adhesives used in the assembly of sandwiched honeycomb structures. Aside from adding weight, the adhesives used to bond honeycomb materials together carry an environmental cost when panel structures are discarded after end of life.
What’s more exciting is the team’s examination of the potential around biopanels – resins made from sugar cane – to replace conventional epoxies used with composites.
The additive manufacturing methods of producing STARLight pieces involves automation and robotics.
Rethinking and retooling structural designs
The journey towards STARLight's realization has not been without hurdles. Chief among them was translating the design of structures so they are optimized for the additive manufacturing process.
Overcoming this challenge of bridging component design to manufacturing required the development of specialized digital tools. These tools enable the optimization of both design and manufacturing processes, accounting for diverse inputs such as configurations and electrical needs.
Game changing implications
Adopting STARLight structural material has far-reaching implications within the cabin, given its weight savings along with customization opportunities. Integration opportunities include galleys, lavatories and seat structures.
Moreover, STARLight represents more than just a material innovation—it embodies a holistic approach to sustainability that could change the industry.
“One aspect of STARLight doesn’t get you there. It’s the end-to-end nature of the entire lifecycle that’s a game changer,” explains St. Rock. “I feel like the term is overused, but with STARLight, we really have a game-changing opportunity. I see our factories looking different.”